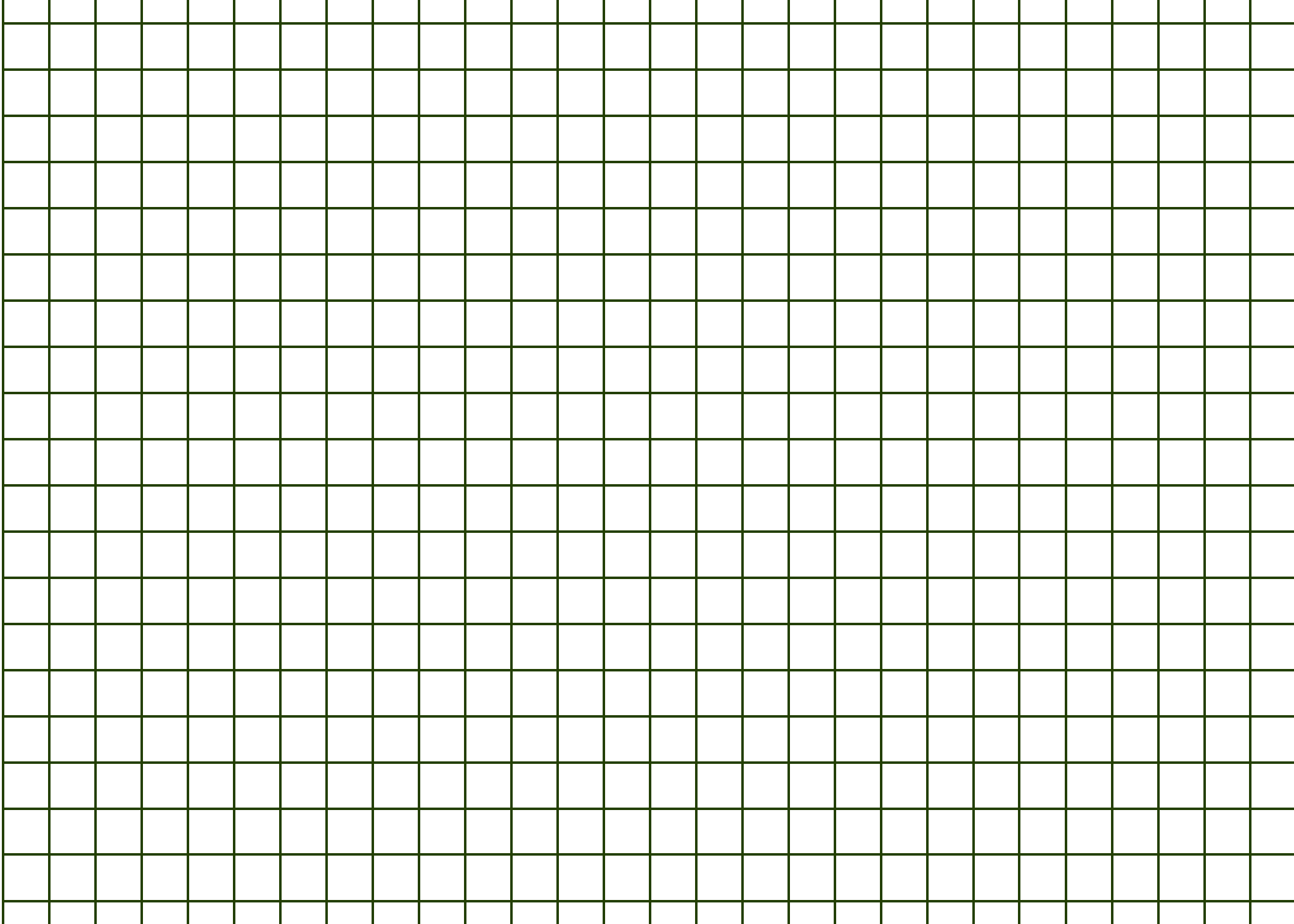
Design #1:
Iterating on Inspiration
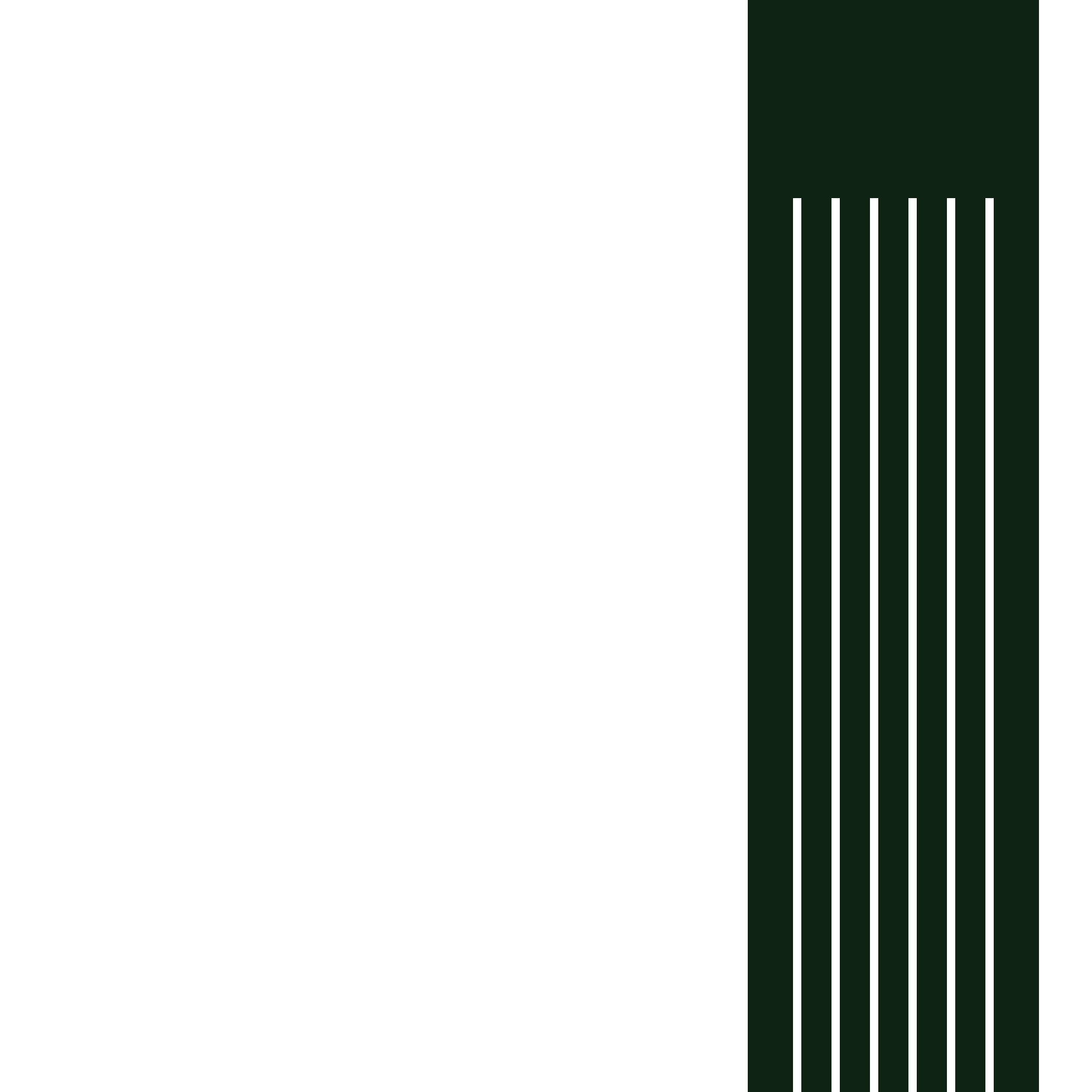
When we began exploring the possibility of starting a furniture business, a natural first question was what kind of furniture we would be making.
To get ideas, we explored some old furniture books my dad inherited from his uncle. The inspiration for our first design came from a 1909 Popular Mechanics handbook on building Mission Furniture.
Our first concept was to base a design on these plans for a Mission Library Table, miniaturizing it for use as a side table.
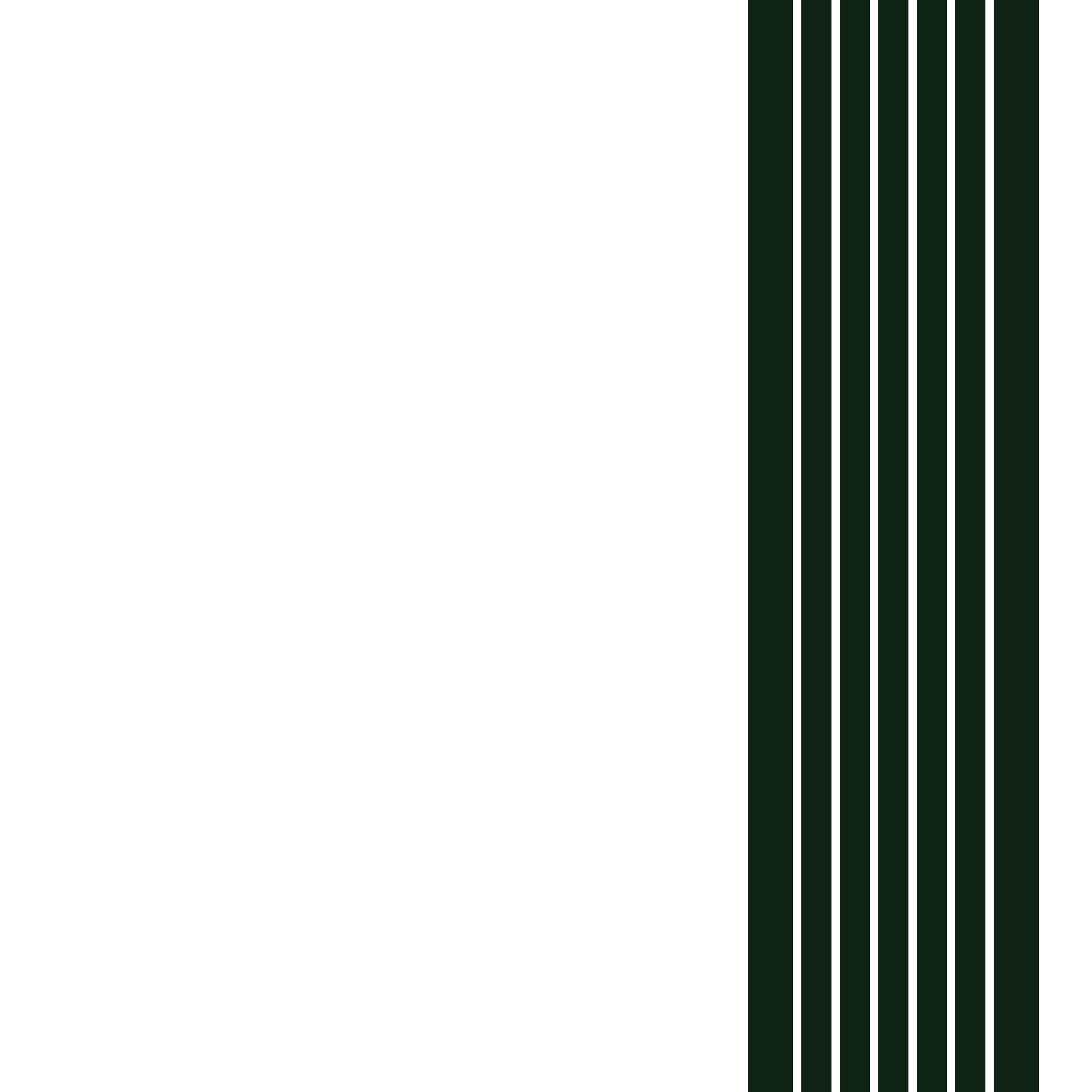
Iterations 1 and 2: Finding the Design
While I would eventually begin learning how to use CAD to accelerate my design process, the first two iterations of this table were designed by hand on paper, after which I would assemble a schematic drawing in Photoshop, modeled off the images in the original book.
We built one prototype of the first design, and three prototypes of the second iteration. Since the table is small, we used it as a low-cost way to test the look and workability of different wood species.
Left to Right: V1 in Pine, V2 in Stained Poplar, V2 in Maple, V2 in Alder
Above: Schematics of Versions 1 and 2
Below: V2 corrections and annotations
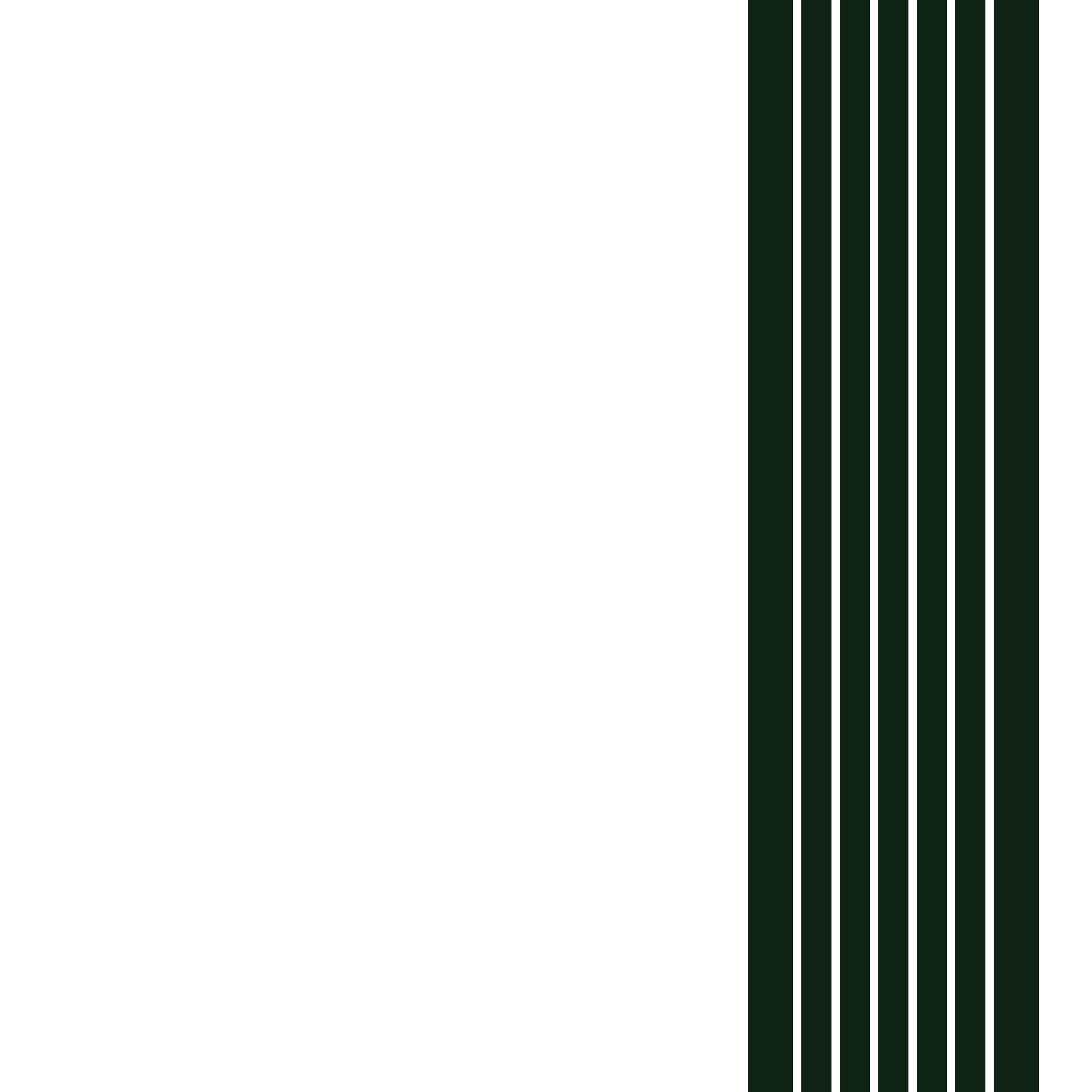
Iteration 3: CAD and Improved Joinery
Versions 1 and 2 feature very rudimentary construction methods, namely lap joints and pocket holes. The methods we used were labor-intensive and produced weak connections, contradicting our goal of heirloom-quality pieces at an accessible price point.
To address both of these problems, we employed a custom mortise-and-tenon joinery method for attaching the legs. These updated joints are simpler to construct, easier to align when being connected, and should be more resistant to the expansion and contraction properties inherent to all solid wood furniture.
Below: V3 in Sapele
Above: A comparison of leg connections in V2 (left) and V3 (right)
Below: CAD of V3 (left), and V3 mortise/tenon schematic (right)
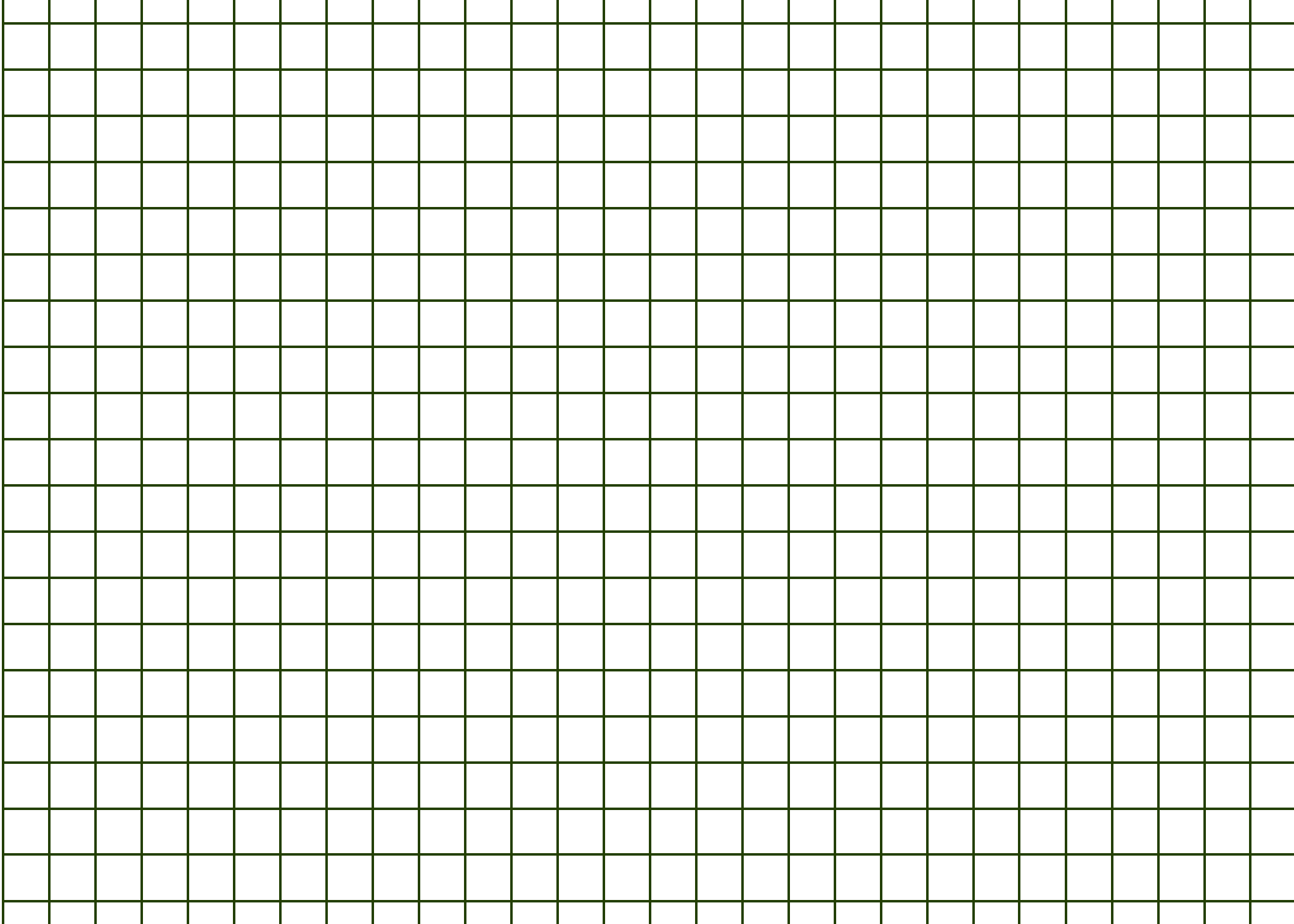
In Conclusion
By The Numbers
Prototypes:
V1: 1
V2: 4
V3: 2
September 2023 - April 2024
7 months development time
Dimensions
18” H x 12 3/4” W x 17” L
Retail Asking Price: $400
What I Learned
Hands-on with the Design/Prototype/Iterate Cycle. While I’ve been learning the fundamentals of the design process since I was 14, school never offers the resources or time required to refine designs to full maturity. While it may be a few years before I can definitively call this design finished, this is the most satisfied I have been with a design up until this point.
Custom jigs + fabrication techniques. Designing for wood is new to me, and the process of iterating on this piece taught me the complexity that comes with a natural material. Designers must anticipate material imperfections, and create designs with a certain level of (1) understanding the fabrication process and (2) tolerance for things to go wrong during building.
The value of time. Time is a necessary element of ensuring a design’s maturity. After V2, we spent months working on other designs before returning to this one, and our growth taught us how V3 could be better.